ASQ – Six Sigma Yellow Belt Interview Questions
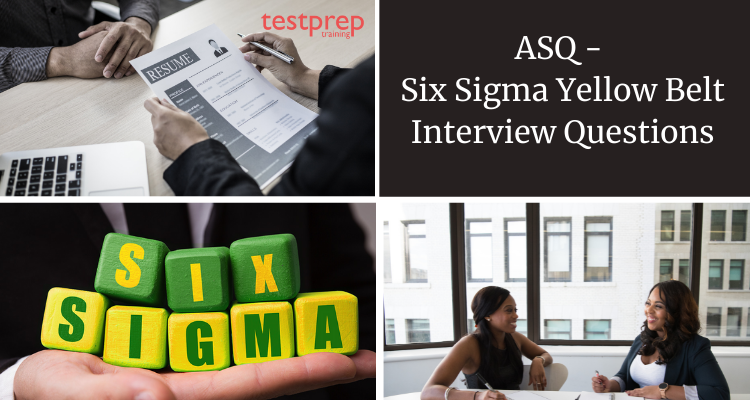
Preparing for an interview is as important as preparing for an exam. Therefore, preparing for an interview takes a lot more practice and confidence to ace any exam. You have to make the best first impression. So to help our candidates to prepare well for the ASQ – Six Sigma Yellow Belt interview, we have tried our best to present you with the best and expert-revised interview questions. Candidates should research the company, job roles, and responsibilities, and most importantly look confident while answering any question. Moreover, we have covered all interview questions from basic to intermediate and to advance levels. Therefore, we highly recommend the aspirants prepare with the best and achieve the best. But first, you should be familiar with the basics of what the ASQ – Six Sigma Yellow Belt exam is all about.
This exam is for candidates who are new to Six Sigma and have a small role, interest or need to develop foundational knowledge. The main point to ponder upon is that the Certified Six Sigma Yellow Belt has no experience or education requirements. Therefore, Yellow belts can also be called entry-level employees who attempt to improve their world or executive upholders who require an overview of Six Sigma and define, measure, analyze, improve and control model (DMAIC). Furthermore, we are here to help our users with the best ASQ – Six Sigma Yellow Belt Interview questions. So, follow us for more updates and ace your exam with flying colors.
Advanced Interview Questions
Can you explain the difference between a process sigma and a project sigma?
A process sigma and a project sigma are related but distinct concepts in Six Sigma. A process sigma is a measure of the performance of a specific process. It is calculated using a formula that takes into account the number of defects per unit of output, and it is expressed in terms of standard deviations from the mean. A process sigma of 6, for example, indicates that a process is operating with only 3.4 defects per million opportunities. The higher the process sigma, the better the process is performing.
A project sigma, on the other hand, is a measure of the performance of a specific Six Sigma project. It is calculated using the same formula as process sigma, but it applies to the specific project rather than to the process as a whole. A project sigma of 6, for example, indicates that the project is achieving Six Sigma performance.
In summary, Process Sigma is a measure of how well a process is performing and Project Sigma is a measure of how well a specific Six Sigma project is performing.
What is a control plan and why is it important?
A control plan in Six Sigma is a document that outlines the procedures and processes that will be used to maintain and sustain improvements made during a Six Sigma project. It is a critical step in the Six Sigma methodology, as it ensures that the improvements made during the project are sustained over time.
A control plan typically includes the following information:
- The process is controlled: This includes a detailed description of the process, including inputs, outputs, and key performance indicators (KPIs).
- The control methods: This includes the specific tools and techniques that will be used to monitor and control the process, such as statistical process control (SPC) charts, process flow diagrams, and checklists.
- The roles and responsibilities: This includes a clear definition of who is responsible for implementing and maintaining the control plan, as well as who will be responsible for monitoring and reporting on the process.
- The monitoring schedule: This includes a schedule for when the process will be monitored and how frequently, as well as the metrics that will be used to measure performance.
- The action plan: This includes a plan for how to respond to any deviations or issues that arise, including corrective actions and process improvements.
The control plan is important because it helps to ensure that the improvements made during a Six Sigma project are sustainable over time. By clearly defining the processes and procedures that will be used to maintain the improvements, it helps to ensure that the process stays in control and that any issues that arise can be quickly identified and addressed. It also provides a roadmap for future process improvement efforts, by identifying the areas of the process that need to be continuously monitored and improved.
How does Six Sigma differ from other quality improvement methodologies?
Six Sigma is a methodology for quality improvement that focuses on reducing defects and variability in processes. It is different from other quality improvement methodologies in several key ways:
- Statistical-based: Six Sigma is based on statistical methods, such as statistical process control (SPC) and design of experiments (DOE), to identify and eliminate the causes of defects and variability in processes. Other methodologies may rely more on intuition and experience to identify problems.
- Data-driven: Six Sigma uses data to drive the improvement process, by collecting and analyzing data to identify and quantify problems, and then using the data to design and implement solutions.
- Continuous improvement: Six Sigma is a continuous improvement methodology, meaning that it is not a one-time event, but rather a continuous process of identifying and eliminating defects and variability.
- Defect reduction: Six Sigma is focused on reducing defects and variability in processes, with the goal of achieving a sigma level of 3.4 or higher (meaning 3.4 defects per million opportunities or less). Other methodologies may have different goals, such as increasing customer satisfaction or reducing costs.
- Leadership: Six Sigma requires strong leadership and commitment from the top level of an organization. This is because Six Sigma is a long-term change process that requires resources and support from the leadership.
Overall, Six Sigma is a data-driven, statistical-based, and continuous improvement methodology that focuses on reducing defects and variability in processes, and requires strong leadership and commitment from the top level of an organization.
Can you give an example of a Six Sigma project you have worked on?
A manufacturing company is experiencing high levels of scrap and rework in its production process. They decide to launch a Six Sigma project to address the problem. The project team, led by a Six Sigma Green Belt, begins by defining the problem and the project objectives. They determine that the goal of the project is to reduce the scrap and rework rate by 50% within the next six months.
Next, the team collects and analyzes data on the production process, identifying the root causes of the scrap and rework. They find that the main causes are poor quality raw materials and outdated equipment. Using the DMAIC process, the team works on the Improve phase, implementing new procedures for sourcing and inspecting raw materials, as well as upgrading equipment. They also train employees on the new procedures.
Finally, the team monitors and controls the process to ensure that the improvements are sustained. They use statistical process control tools to keep track of the scrap and rework rate and make adjustments as needed. As a result of the project, the scrap and rework rate is reduced by 55% in just six months. The company saves a significant amount of money by reducing waste and increasing efficiency.
This is a simple example of a Six Sigma project that utilizes the DMAIC process to improve a specific aspect of a process, in this case, the scrap and rework rate.
How do you measure the success of a Six Sigma project?
Measuring the success of a Six Sigma project is important to determine the effectiveness of the project and the return on investment. There are several key metrics that can be used to measure the success of a Six Sigma project, including:
- Defects per million opportunities (DPMO): This metric measures the number of defects in a process, and is commonly used to measure the quality of a process. The lower the DPMO, the better the quality of the process.
- Process sigma level: This metric measures the level of process capability, and is calculated based on the DPMO. The higher the process sigma level, the better the process capability.
- Cycle time: This metric measures the time it takes for a process to complete one cycle, and is used to measure the efficiency of a process.
- Customer satisfaction: This metric measures the level of satisfaction of the customers, and is used to measure the effectiveness of the process from the customer’s perspective.
- Cost savings: This metric measures the financial benefits of the project, including any cost savings or increased revenue resulting from the project.
- Return on Investment (ROI): This metric measures the financial benefits of the project, including any cost savings or increased revenue resulting from the project, in relation to the investment made in the project.
- Process Performance Index (PPI): This metric measures the efficiency and effectiveness of the process, and is calculated as the ratio of process performance to process capability.
It is also important to consider other factors such as employee engagement, process flow, and process stability. By measuring these metrics, you can determine the overall success of the Six Sigma project and the impact it has had on the organization.
How can Six Sigma be integrated into an organization’s overall strategy?
Six Sigma can be integrated into an organization’s overall strategy in several ways:
- Alignment with business objectives: Six Sigma should be aligned with the organization’s overall business objectives, such as increasing customer satisfaction, reducing costs, or improving efficiency. This ensures that the improvement efforts are focused on areas that are critical to the organization’s success.
- Leadership commitment: Six Sigma requires strong leadership and commitment from the top level of an organization. Top-level executives should be involved in the implementation and oversight of the Six Sigma program.
- Training and development: Six Sigma requires a skilled workforce to implement and maintain improvement efforts. Employees should be trained in Six Sigma methodology and tools and provided with ongoing development opportunities.
- Process improvement: Six Sigma uses data-driven and statistical methods to identify and eliminate the causes of defects and variability in processes. This can be integrated into the organization’s overall process improvement strategy.
- Metrics and measurement: Six Sigma uses metrics and measurement to track progress and measure the success of improvement efforts. These metrics should be integrated into the organization’s overall performance measurement system.
- Continuous improvement: Six Sigma is a continuous improvement methodology, meaning that it is not a one-time event, but rather a continuous process of identifying and eliminating defects and variability. This can be integrated into the organization’s overall continuous improvement strategy.
Overall, Six Sigma should be integrated into an organization’s overall strategy by aligning with business objectives, obtaining leadership commitment, providing training and development, integrating process improvement, integrating metrics and measurement, and integrating continuous improvement.
How do you prioritize potential Six Sigma projects within an organization?
There are several ways to prioritize potential Six Sigma projects within an organization. Some common methods include:
- Impact and feasibility: Projects are evaluated based on their potential impact on the organization and their feasibility. Projects with high impact and high feasibility are given priority.
- Cost-benefit analysis: Projects are evaluated based on their potential return on investment (ROI). Projects with the highest ROI are given priority.
- Voice of the customer: Projects are prioritized based on feedback from customers. Projects that address customer complaints or requests are given priority.
- Critical to Quality (CTQ) Tree: By utilizing the CTQ tree, an organization can evaluate projects based on their impact on critical quality characteristics, and prioritize projects that have the biggest impact on CTQs.
- Data-driven methods: Utilize data analysis to determine which process or area of the business is causing the most issues, and prioritize projects that address those areas.
- Align with strategic goals: Prioritize projects that align with the organization’s overall strategy and goals.
It’s important to note that not all these methods need to be used in isolation, rather a combination of these methods can be used to prioritize the projects. The key is to ensure that the chosen method is relevant to the organization and that it aligns with the overall goals of the organization.
How do you ensure that the gains from a Six Sigma project are sustained over time?
Ensuring that the gains from a Six Sigma project are sustained over time is critical to the success of the project. Here are several key steps that can be taken to ensure sustainability:
- Develop a control plan: A control plan is a document that outlines the procedures and processes that will be used to maintain and sustain the improvements made during the project. The control plan should include a schedule for monitoring the process, a plan for responding to deviations, and a clear definition of roles and responsibilities.
- Implement statistical process control (SPC) methods: SPC methods, such as control charts, are used to monitor the process and detect any changes or deviations from the process. This helps to ensure that the process stays in control and that any issues that arise can be quickly identified and addressed.
- Conduct regular audits: Regular audits of the process can help to ensure that the improvements are being sustained and that the process is performing as expected. Audits can also help to identify any potential issues or areas for improvement.
- Communicate and train: It is important that all employees are aware of the improvements and understand their role in maintaining them. Training and communication can help to ensure that employees understand the process and how to maintain the improvements.
- Continuously monitor and improve: Continuous improvement is a key element of Six Sigma. By monitoring and analyzing the process, you can identify areas for improvement and take steps to continuously improve the process.
- Make process improvement a part of the culture: Making process improvement a part of the culture is key to sustainability. By encouraging employees to be involved in process improvement, and by recognizing and rewarding their contributions, you can create a culture of continuous improvement.
By taking these steps, you can help to ensure that the gains from a Six Sigma project are sustained over time and that the process continues to perform at the highest level.
How do you communicate the progress and results of a Six Sigma project to stakeholders?
Communicating the progress and results of a Six Sigma project to stakeholders is an important aspect of the project, as it helps to keep stakeholders informed and engaged, and helps to ensure that the project stays on track. Here are several key steps that can be taken to communicate the progress and results of a Six Sigma project to stakeholders:
- Hold regular project update meetings: Regular project update meetings are an effective way to keep stakeholders informed of the project’s progress and to address any concerns or issues that may arise.
- Use data visualization tools: Visualizing data can help to make it easier for stakeholders to understand the project’s progress and results. Tools such as graphs, charts, and dashboards can be used to present data in a clear and concise manner.
- Provide written reports: Written reports can be used to provide detailed information on the project’s progress and results. These reports can be shared with stakeholders and can be used to document the project’s progress and results for future reference.
- Communicate the results in business terms: Communicating the results of the project in business terms can help to ensure that stakeholders understand the impact of the project on the organization and the benefits it will bring.
- Use a communication plan: A communication plan can help to ensure that all stakeholders are informed of the project’s progress and results and that the information is provided in a consistent and timely manner.
- Share success stories and case studies: Sharing success stories and case studies can help to demonstrate the value of the project and to build support for the project among stakeholders.
By communicating the progress and results of the Six Sigma project in a clear and consistent manner, you can help to ensure that stakeholders are informed and engaged and that the project stays on track.
How do you handle resistance to change when implementing Six Sigma in an organization?
Handling resistance to change when implementing Six Sigma in an organization can be a challenge. Here are a few strategies that can help:
- Communicate effectively: Communicate the goals and benefits of Six Sigma clearly and consistently to all stakeholders. Share success stories from other organizations that have implemented Six Sigma.
- Involve employees: Encourage employees to participate in Six Sigma training and project work. Give them a sense of ownership in the process and the opportunity to provide feedback.
- Address concerns: Address any concerns or objections that employees may have about Six Sigma. Provide answers to their questions and address their fears.
- Lead by example: Show employees that leadership is committed to Six Sigma by leading by example. Encourage leaders to participate in Six Sigma training and to lead Six Sigma projects.
- Provide training and support: Provide employees with the training and support they need to be successful. This includes not only Six Sigma training but also training on new tools, procedures, and technologies that will be used.
- Recognize and reward success: Recognize and reward employees for their contributions to Six Sigma projects. This helps to create a positive culture of continuous improvement.
- Be patient: Change takes time and it is important to be patient. The implementation of Six Sigma is a journey and not a one-time event.
Ultimately, it is important to remember that resistance to change is normal and to be prepared for it. By communicating effectively, involving employees, addressing concerns, leading by example, providing training and support, recognizing and rewarding success and being patient, organizations can successfully overcome resistance and implement Six Sigma effectively.
Basic Interview Questions
1. What is six sigma?
Six Sigma is defined as a method that provides organizations tools to improve the ability of their business processes. This increase in performance and decrease in process variation helps lead to defect reduction and improvement in profits, employee morale, and quality of products or services.
2. Describe the philosophical view of Six Sigma?
Six Sigma is a data-driven and statistically-based approach to quality management that is grounded in a philosophy of continuous improvement and elimination of defects. It is based on the following key philosophical principles:
- Customer Focus: Six Sigma places the customer at the center of all its activities and aims to deliver products and services that meet or exceed their expectations.
- Data-Driven Decision Making: Six Sigma relies on data and statistical analysis to identify problems, measure progress, and make informed decisions.
- Continuous Improvement: Six Sigma is a never-ending process of identifying areas for improvement and making incremental changes to processes and products to eliminate defects and improve quality.
- Empowerment: Six Sigma empowers employees to identify and solve problems, promoting a culture of continuous improvement.
- Collaboration: Six Sigma encourages cross-functional teams to work together to identify and solve problems, leveraging the collective knowledge and expertise of employees from different areas of the organization.
In summary, the philosophical view of Six Sigma is centered on delivering high-quality products and services, making data-driven decisions, and fostering a culture of continuous improvement and collaboration.
3. Describe the set tools used by Six Sigma experts?
The set of tools used by Six Sigma experts include:
- DMAIC (Define, Measure, Analyze, Improve, Control) – a problem-solving approach used to improve business processes.
- Statistical Process Control (SPC) – used to monitor and control process performance.
- Design of Experiments (DOE) – used to identify the factors affecting a process and determine the optimal combination of these factors.
- Value Stream Mapping (VSM) – used to visually map out the flow of materials and information in a process.
- Failure Modes and Effects Analysis (FMEA) – used to identify potential failures in a process and the consequences of those failures.
- Control Charts – used to monitor and control process performance over time.
- Pareto Charts – used to prioritize improvement efforts by identifying the most critical issues.
- Ishikawa Diagrams (Fishbone Diagrams) – used to identify the root cause of a problem.
- Five S (Sort, Simplify, Sweep, Standardize, Sustain) – a tool used to improve the organization and cleanliness of a workspace.
These tools are used by Six Sigma experts to analyze processes, identify areas for improvement, and implement changes that lead to improved quality and efficiency.
4. Explain the methodology of Six Sigma?
This perspective on Six Sigma comprehends the basic and stringent DMAIC method. DMAIC outlines the procedures a Six Sigma professional must follow, commencing with identifying the issue and concluding with the execution of permanent solutions. Although DMAIC is not the solitary Six Sigma methodology utilized, it is certainly the most commonly embraced and acknowledged.
5. What is Statistical process control (SPC)?
Statistical process control (SPC) is defined as the use of statistical techniques to control a process or production method. Moreover, SPC tools and procedures can help you monitor process behavior, discover issues in internal systems, and find solutions for production issues.
6. What do you understand by the control chart?
The control chart is a graph used to study how a process changes over time. It is also known as the Shewhart chart, a statistical process control chart. Additionally, a control chart always has a central line for the average, an upper line for the upper control limit, and a lower line for the lower control limit.
7. What do you understand by Failure modes and effects analysis?
- The term “failure modes” refers to the different ways in which a product or system might malfunction. This includes any defects or errors that could impact the customer, whether they have already occurred or are potential.
- “Effects analysis” involves examining the results of these failures, and looking at the impact they have.
8. What is Lean Six Sigma?
Lean Six Sigma is a fact-based, data-driven theory of improvement that values defect prevention over defect detection. It arouses customer satisfaction and bottom-line results by reducing variation, waste, and cycle time.
9. List the available options to an organization after implementing Six Sigma?
After the implementation of Six Sigma, an organization has two basic options:
- Firstly, Implement a Six Sigma program or initiative
- Lastly, Create a Six Sigma infrastructure
10. Mention the Six Sigma deployment benefits via projects?
- Increased efficiency and productivity: Six Sigma projects aim to streamline processes, eliminate waste and improve overall performance, leading to increased efficiency and productivity.
- Improved customer satisfaction: Six Sigma projects focus on identifying and resolving the root cause of customer complaints and issues, resulting in improved customer satisfaction.
- Enhanced quality: Six Sigma projects are designed to improve quality by eliminating defects and improving the overall quality of products and services.
- Increased profitability: Six Sigma projects result in cost savings, increased efficiency, and improved customer satisfaction, leading to increased profitability for the organization.
- Better decision making: Six Sigma projects use data-driven methods to make informed decisions, resulting in better outcomes for the organization.
- Improved employee engagement: Six Sigma projects encourage employee involvement, leading to increased employee engagement and a more positive work environment.
- Better risk management: Six Sigma projects help organizations identify and mitigate potential risks, resulting in improved risk management and a more secure working environment.
- Increased competitiveness: Six Sigma projects result in improved efficiency and quality, leading to increased competitiveness in the market.
- Better supplier management: Six Sigma projects help organizations establish better relationships with suppliers, resulting in improved supplier management and reduced supply chain disruptions.
- Improved sustainability: Six Sigma projects encourage the use of sustainable practices, reducing waste and helping organizations to meet their sustainability goals.
11. Define and describe the roles and responsibilities of Six Sigma team members?
- Master Black Belt: Trains and coaches Black Belts and Green Belts. Acts as an organization’s Six Sigma technologist and internal consultant.
- Black Belt: Leads problem-solving projects. Trains and coaches project teams.
- Green Belt: Assists with data collection and analysis for Black Belt projects. Leads Green Belt projects or teams.
- Yellow Belt: Participates as a project team member. Reviews process improvements that support the project.
- White Belt: Can participate in local problem-solving teams that contribute to larger projects, but may not be involved in a formal Six Sigma project team. Additionally, has a basic understanding of Six Sigma principles from an informational standpoint.
- Brown Belt: A Brown Belt designation is not a standard in the Six Sigma methodology and is not widely accepted by most organizations or accreditation bodies. However, some companies may categorize a Brown Belt as an individual who holds a Green Belt certification and has passed the Black Belt exam, but has not yet completed a second Six Sigma project.
12. Explain the role of Champions?
Translate the company’s vision, mission, goals, and metrics to create an organizational deployment plan and identify individual projects. Moreover, they identify resources and remove roadblocks.
13. Explain the role of Executives?
Provide overall alignment by establishing the strategic focus of the Six Sigma program within the context of the organization’s culture and vision.
14. What is a Team?
A team refers to a collection of individuals who collaborate on interrelated tasks with the aim of achieving a shared goal or purpose.
15. List the different types of Teams?
The three types of Teams are listed as follow:
- Firstly, Process Improvement Teams
- Then, Work Groups or Natural Teams
- Lastly, Self-Managed Teams
16. Describe the Process Improvement Teams?
Team dedicated to enhancing business processes, known as process improvement teams, focus on enhancing or creating specific business procedures. These teams assemble with a particular objective in mind, adhere to a clear project plan, and have a defined starting and conclusion point through agreement.
17. Explain the Work Groups or Natural Teams?
Workgroups are accountable for a specific process and collaborate in a participatory setting. The participatory methodology is rooted in the idea that increased responsibility for their tasks will lead to enhanced productivity among employees.
18. Describe Self-Managed Teams?
In a self-managed team setting, the daily operation of a specific process or department is managed by the team members themselves. They are given the freedom to make decisions related to various aspects including safety, quality, maintenance, scheduling, and personnel. These teams also undertake responsibilities that are typically performed by managers, such as setting goals, assigning tasks, and resolving conflicts.
19. List the benefits Team processes offer to the organization?
- Synergistic process design or problem solving
- Objective analysis of problems or opportunities
- Promotion of cross-functional understanding
- Improved quality and productivity
- Greater innovation
- Reduced operating costs
- Increased commitment to organizational mission
- More flexible response to change
- Increased ownership and stewardship
- Reduced turnover and absenteeism
20. List the benefits Individuals can gain from the teams?
- Enhanced problem-solving skills
- Increased knowledge of interpersonal dynamics
- Broader knowledge of business processes
- New skills for future leadership roles
- Increased quality of work life
- Feelings of satisfaction and commitment
- A sense of being part of something greater than what one could accomplish alone
21. What is the use of Multivoting?
Multivoting narrows a large list of possibilities to a smaller list of the top priorities or a final selection. It also allows an item that is favored by all, but not the top choice of any, to rise to the top.
22. Give some reasons why Teams fail?
- Lack of Clear Goals and Objectives: Teams can fail if they do not have a clear understanding of what they are trying to achieve, leading to confusion and lack of direction.
- Communication Breakdowns: Teams that struggle with communication, whether it is a lack of clarity or conflict between members, will not be able to work effectively together.
- Lack of Trust and Cooperation: Teams that lack trust and cooperation will struggle to work effectively together, leading to lack of progress and dissatisfaction among team members.
- Poor Leadership: Teams can fail if they do not have effective leadership to guide and motivate them, leading to a lack of direction and accountability.
- Resistance to Change: Teams can also fail if they are resistant to change and unwilling to adapt to new ideas and processes, leading to a lack of innovation and growth.
23. Define Quality tools?
Quality tools are termed as an instrument or technique to support and improve quality management and improvement activities.
24. What are Stakeholders?
Stakeholders may include suppliers, internal staff, members, customers, regulators, and local and regional communities. Additionally, stakeholders may include purchasers, clients, owners, and non-governmental organizations (NGOs).
25. Define Stakeholder analysis?
Stakeholder analysis is defined as a tool organization can apply to clearly recognize key stakeholders for a project or other activity, understand where stakeholders stand, and develop collaboration between the stakeholders and the project team.
26. Mention different types of Stakeholders?
Types of stakeholders include:
- Primary: Those who are directly affected, either positively or negatively, by an organization’s actions.
- Secondary: Those who are indirectly affected by an organization’s actions.
27. List the Benefits of creating a Stakeholder Analysis?
- Firstly, Provides clear understanding of stakeholders’ interests
- Offers mechanisms to influence other stakeholders
- Enables full understanding of potential risks
- Identifies key people to be updated regarding the project during the execution phase
- Finally, creates an understanding of hostile stakeholders and the negative impact they may have on the project.
28. Explain the Project planning tools?
Project planning tools are defined as a series of systems and methodologies designed to ensure teams can accomplish both short- and long-term projects. Project planning tools include charts and graphs designed to follow progress, repetition-based access to testing and adjusting everyday processes, and other actions that allow organizations to manage and improve critical projects.
29. Define Gage repeatability and reproducibility (GR&R)?
Gage repeatability and reproducibility (GR&R) is defined as a process used to evaluate a gauging instrument’s accuracy by ensuring its measurements are repeatable and reproducible.
30. What is DMADV?
Define, Measure, Analyze, Design, and Verify (DMADV) is a data-driven quality strategy that concentrates on the development of new products or services related to existing ones.
31. Mention the three types of GR&R studies?
- Crossed GR&R Study
- Nested GR&R Study
- Expanded GR&R Study
32. What is a Root cause analysis(RCA)?
Root cause analysis, abbreviated as RCA, refers to a group of methods, tools, and techniques utilized to determine the origin of issues.
33. What is the Law of Variation?
The Law of Variation is defined as the difference between an idea and an actual situation. Variation or variability is most frequently met as a change in data, expected outcomes, or slight changes in production quality.
34. Where can you see Variations?
Variation usually occurs in four separate areas:
- Firstly, Special causes
- Secondly, Common causes
- Thirdly, Tampering
- Lastly, Structural variation
35. When to use the PDCA Cycle?
Use the PDCA cycle when:
- When starting a new project or initiative: The PDCA cycle can be used as a framework to guide the planning and implementation of a new project or initiative.
- When introducing a new product or service: The cycle can be used to assess and evaluate the success of a new product or service.
- When solving a problem or addressing a challenge: The cycle can help organizations systematically identify and solve problems or challenges by evaluating and improving processes.
- When making changes or improvements to existing processes: The PDCA cycle can be used to evaluate and implement changes or improvements to existing processes.
- When monitoring and evaluating performance: The cycle can be used to regularly monitor and evaluate performance, allowing organizations to identify areas for improvement and make necessary adjustments.
36. When to use a Control chart?
Use the Control chart when:
- Controlling ongoing processes by finding and correcting problems as they occur
- Predicting the expected range of outcomes from a process
- Determining whether a process is stable (in statistical control)
- Analyzing patterns of process variation from special causes (non-routine events) or common causes (built into the process)
- Determining whether your quality improvement project should aim to prevent specific problems or to make fundamental changes to the process
37. What is DMAIC?
Define, measure, analyze, improve, and control (DMAIC) is a data-driven quality strategy technique to improve processes. Moreover, it is an integral part of a Six Sigma quality initiative.
38. Mention the S’S?
- Seiri
- Seiton
- Seiketsu
- Shitsuke
- Seiso
39. List the benefits of 5S?
- Improved safety
- Higher equipment availability
- Lower defect rates
- Lesser costs
- Increased production agility and flexibility
- Improved employee morale
- Better asset utilization
- Enhanced enterprise image to customers, suppliers, employees, and management
40. What is a quality plan?
A quality plan is a document, or several documents, that collectively specify quality standards, practices, resources, specifications, and the sequence of activities relevant to a particular product, service, project, or contract.