Lean Six Sigma Yellow Belt Certification (LSSYB) Sample Questions
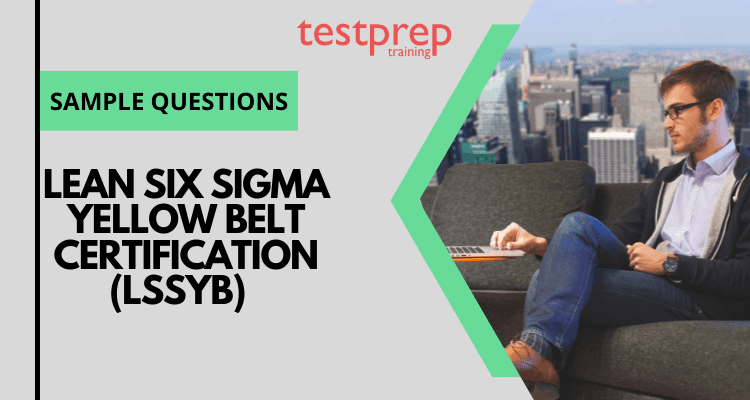
A Certified Lean Six Sigma Yellow Belt from the Council for Six Sigma Certification (CSSC) is someone who has mastered the fundamentals of Six Sigma. They are frequently in charge of creating method maps to aid Six Sigma projects. A Yellow Belt competes on a project or projects as a core team member or subject matter expert (SME).
Yellow Belts are frequently responsible for managing smaller process improvement projects using the PDCA (Plan, Do, Check, Act) methodology. PDCA, also known as the Deming Wheel, guides Yellow Belts in identifying methods that can aid in improvement. Smaller Yellow Belt projects are frequently escalated to the Green Belt or Black Belt levels, where a DMAIC methodology is used to maximize cost savings through Statistical Process Control.
Advanced Sample Questions
What is Lean Six Sigma?
- A) A process improvement method that combines elements of both Lean and Six Sigma.
- B) A method for improving the efficiency of business processes.
- C) A tool for analyzing data and identifying problems in a process.
Answer: A) A process improvement method that combines elements of both Lean and Six Sigma.
Explanation: Lean Six Sigma is a process improvement method that combines elements of both Lean and Six Sigma. Lean focuses on reducing waste and maximizing efficiency, while Six Sigma focuses on data-driven problem solving and process improvement. Together, Lean Six Sigma provides a comprehensive approach to process improvement, helping organizations identify and eliminate waste, improve efficiency, and increase customer satisfaction.
What is a DMAIC process?
- A) A tool for analyzing data and identifying problems in a process.
- B) A method for measuring the performance of a process.
- C) A structured approach for improving a process using data and statistical analysis.
Answer: C) A structured approach for improving a process using data and statistical analysis.
Explanation: DMAIC is a structured approach for improving a process using data and statistical analysis. It stands for Define, Measure, Analyze, Improve, and Control, and is one of the core methodologies used in Lean Six Sigma. DMAIC provides a systematic approach for identifying and solving problems in a process, using data-driven decision making to identify areas for improvement, implement changes, and monitor progress.
What is a Lean methodology?
- A) A process improvement method that combines elements of both Lean and Six Sigma.
- B) A method for reducing waste and maximizing efficiency in business processes.
- C) A tool for analyzing data and identifying problems in a process.
Answer: B) A method for reducing waste and maximizing efficiency in business processes.
Explanation: Lean is a methodology for reducing waste and maximizing efficiency in business processes. It focuses on identifying and eliminating waste in a process, including activities that do not add value to the customer, and streamlining processes to increase efficiency. The goal of Lean is to create a continuous flow of work that is free of bottlenecks and other obstacles, resulting in improved process performance and increased customer satisfaction.
What is the purpose of the Six Sigma methodology?
- A) To improve the efficiency of business processes.
- B) To reduce waste and maximize efficiency in business processes.
- C) To use data-driven decision making to identify and solve problems in a process.
Answer: C) To use data-driven decision making to identify and solve problems in a process.
Explanation: Six Sigma is a methodology that uses data-driven decision making to identify and solve problems in a process. It focuses on collecting and analyzing data to identify areas for improvement, and using statistical analysis to determine the root cause of problems and implement effective solutions. The goal of Six Sigma is to improve the quality and efficiency of processes, reduce defects and errors, and increase customer satisfaction.
What is a Value Stream Map (VSM)?
- A) A graphical representation of a process that shows the flow of material, information, and activities.
- B) A tool for measuring the performance of a process.
- C) A structured approach for improving a process using data and statistical analysis.
Answer: A) A graphical representation of a process that shows the flow of material, information, and activities.
Explanation: A Value Stream Map (VSM) is a graphical representation of a process that shows the flow of material, information, and activities. It is used in Lean methodology to identify waste in a process and to develop strategies for improvement. A VSM provides a visual representation of the process, including the flow of materials and information, the time it takes to complete each step, and any bottlenecks or other obstacles that may impact the process. By using a VSM, organizations can identify areas for improvement and develop strategies to eliminate waste and improve process efficiency.
What is a Control Plan?
- A) A plan for monitoring and maintaining the improvements made in a process.
- B) A tool for analyzing data and identifying problems in a process.
- C) A method for reducing waste and maximizing efficiency in business processes.
- Answer: A) A plan for monitoring and maintaining the improvements made in a process.
Explanation: A Control Plan is a plan for monitoring and maintaining the improvements made in a process. It is a key component of the Control phase of the DMAIC process in Lean Six Sigma. A Control Plan outlines the steps that will be taken to monitor and maintain the improvements made in a process, including who will be responsible for monitoring the process, what metrics will be used to measure progress, and how the process will be maintained over time. By using a Control Plan, organizations can ensure that the benefits of process improvements are sustained over time, resulting in long-term process improvement and increased customer satisfaction.
What is a Control Chart?
- A) A graphical representation of a process that shows the flow of material, information, and activities.
- B) A tool for monitoring and maintaining the improvements made in a process.
- C) A chart used to track process performance over time and identify trends and patterns.
Answer: C) A chart used to track process performance over time and identify trends and patterns.
Explanation: A Control Chart is a chart used to track process performance over time and identify trends and patterns. It is a key tool used in Lean Six Sigma to monitor the performance of a process and ensure that improvements are sustained over time. A Control Chart plots process performance data over time, providing a visual representation of process performance and allowing organizations to identify trends and patterns in the data. By using a Control Chart, organizations can identify changes in process performance that may indicate the need for further improvement, and take action to sustain the improvements made in a process.
What is a Fishbone Diagram (Ishikawa Diagram)?
- A) A tool for reducing waste and maximizing efficiency in business processes.
- B) A diagram used to identify the root cause of a problem.
- C) A graphical representation of a process that shows the flow of material, information, and activities.
Answer: B) A diagram used to identify the root cause of a problem.
Explanation: A Fishbone Diagram (Ishikawa Diagram) is a diagram used to identify the root cause of a problem. It is a key tool used in Lean Six Sigma to identify potential causes of a problem and to develop strategies for improvement. A Fishbone Diagram shows the relationship between a problem and its potential causes, and helps organizations to identify the root cause of a problem by analyzing the data and breaking down the problem into smaller parts. By using a Fishbone Diagram, organizations can identify areas for improvement, prioritize the causes of a problem, and develop strategies to eliminate waste and improve efficiency.
What is a Process Flow Diagram (PFD)?
- A) A chart used to track process performance over time and identify trends and patterns.
- B) A diagram used to identify the root cause of a problem.
- C) A graphical representation of a process that shows the flow of material, information, and activities.
Answer: C) A graphical representation of a process that shows the flow of material, information, and activities.
Explanation: A Process Flow Diagram (PFD) is a graphical representation of a process that shows the flow of material, information, and activities. It is used in Lean methodology to understand and improve the flow of a process. A PFD provides a visual representation of the process, including the flow of materials and information, the time it takes to complete each step, and any bottlenecks or other obstacles that may impact the process. By using a PFD, organizations can identify areas for improvement and develop strategies to eliminate waste and improve process efficiency.
What is a Statistical Process Control (SPC)?
- A) A method for reducing waste and maximizing efficiency in business processes.
- B) A tool for monitoring and maintaining the improvements made in a process.
- C) A statistical technique used to monitor and control a process by analyzing data.
Answer: C) A statistical technique used to monitor and control a process by analyzing data.
Explanation: Statistical Process Control (SPC) is a statistical technique used to monitor and control a process by analyzing data. It is a key tool used in Lean Six Sigma to improve process performance and ensure that improvements are sustained over time. SPC involves analyzing data from a process to identify patterns and trends, and then using this information to monitor and control the process. By using SPC, organizations can identify changes in process performance that may indicate the need for further improvement, and take action to sustain the improvements made in a process.
Basic Sample Questions
Lean Six Sigma Yellow Belt Certification (LSSYB) Sample Questions
Question 1 –
When a process has been demonstrated to function at the Six Sigma level, it means that there are fewer than _ defects per million opportunities.
- A. 2.6
- B. 1.7
- C. 3.4
- D. 10
Correct Answer –C
Question 2 –
Six Sigma denotes a process in which at least 95% of its data points are within 6 standard deviations of the mean.
- A. True
- B. False
Correct Answer –B
Question 3 –
Training costs $3,000, and a project requires a $20,000 initial investment. What is the payback period in months (before money costs and taxes) if the project produces monthly savings of $1,800 after 3 months?
- A. 8.33
- B. 4.17
- C. 11.33
- D. 28.28
Correct Answer –C
Question 4 –
A project’s ROI is a measurement metric that stands for Return on Investment and is one of the methods used to assess the success of a Lean Six Sigma project.
- A. True
- B. False
Correct Answer –A
Question 5 –
The DMAIC problem-solving approach stands for Define, __, Analyze, Improve, and Control.
- A. Memorize
- B. Measure
- C. Manage
- D. Manipulate
Correct Answer –B
Question 6 –
Voice of the Customer is a Lean Six Sigma technique for determining a product’s or service’s __ attributes.
- A. Desirable
- B. Beneficial
- C. Critical-to-Quality
- D. Preferred
Correct Answer –C
Question 7 –
Which of the following would be most concerned with benefits and working conditions?
- A. Voice of the Customer
- B. Voice of the Employee
- C. Voice of the Process
- D. Voice of the Business
Correct Answer –B
Question 8 –
Y, the output, is the _ variable in the expression Y = f(Xn), and Xn, the inputs, are the variables.
- A. Independent, dependent
- B. Individual, multiple
- C. Sole, multiple
- D. Dependent, independent
Correct Answer –D
Question 9 –
We attempt to determine the gaps in our processes between ‘what is’ and _____ when we assess the Voice of the Customer.
- A. ג€What isn’tג€
- B. ג€What will make moneyג€
- C. ג€What will cost lessג€
- D. ג€What should beג€
Correct Answer –D
Question 10 –
Which of the following is unlikely to be a CTQ (Critical-to-Quality) for product purchase?
- A. Durability
- B. Functionality
- C. Dependability
- D. None
Correct Answer –D
Question 11 –
The Pareto Chart is a tool that displays data that usually follows what ratio?
- A. 70:30
- B. 80:20
- C. 90:10
- D. 95:5
Correct Answer –B
Question 12 –
Al purchased a handheld GPS from his neighborhood electronics store. When he entered an address, it did not work. This would be classified as what type of cost for the GPS manufacturer.
- A. Prevention Cost
- B. Internal Failure Cost
- C. External Failure Cost
- D. Appraisal Cost
Correct Answer –C
Question 13 –
Which of the following is a method of expressing the concept that a process’s outputs are a function of all of its inputs?
- A. Y = f(Xn)
- B. Yield = Effort
- C. RTY > 90%
- D. Flow = Demand
Correct Answer –A
Question 14 –
When creating a Process Map, we would use the _ symbol to represent an action step in the process.
- A. Ellipse
- B. Circle
- C. Diamond
- D. Rectangle
Correct Answer –D
Question 15 –
A Belt has determined that the loan application does not need to be reviewed by accounting, allowing a loan processer to handle more applications. RTY improvement would be considered __ under Cost of Poor Quality (COPQ) definitions.
- A. Downsizing savings
- B. Hard savings
- C. Soft savings
- D. Median savings
Correct Answer –B
Question 16 –
The following Business Case is properly constructed.
‘During the majority of 2008, Division 16 experienced a 4.2% product return rate, compared to a target of nearly no returns.’ This costs the company a lot of money.
- A. True
- B. False
Correct Answer –B
Question 17 –
The essence of Lean is to focus on _______ while improving process flow in order to achieve speed and agility at a lower cost.
- A. Defect removal
- B. Removing waste
- C. Rework reduction
- D. Overtime reduction
Correct Answer –B
Question 18 –
As Belt created a Process Map, he realized there were multiple departments involved in this process, so he added a feature called _ to the map.
- A. Department Dividers
- B. Swim Lanes
- C. Passing Lanes
- D. Responsibility Paths
Correct Answer –B
Question 19 –
One of the primary goals in developing and defining an LSS project is to reduce the__
- A. Inventory
- B. Number of process steps
- C. Work force
- D. Cost of Poor Quality
Correct Answer –D
Question 20 –
In an organization, the Value Chain is the sum of all the processes that occur in the business to take inputs and turn them into customer desired outputs.
- A. True
- B. False
Correct Answer –A